<
山口恵里の“現場に行く!”2024年7月号
「第60回 コニテク株式会社(ゼミKYOTO会社見学会)」
皆さん、こんにちは!スモールサン事務局の山口恵里です。
「山口恵里の“現場に行く!”」第60回は、京都市下京区にあるコニテク株式会社の代表取締役社長、松田 裕さんにお話をお聞きしました!
この日は、ゼミKYOTOでの会社見学企画の第1回ということで、私も同行させていただきました!
工作機械で使用される「切削液」というものはご存知ですか?
切削加工をする際に切削箇所に吹きかけられる液体で、これは繰り返し使用された後に廃棄・交換されるのだそうです。使用を繰り返す中でスラッジという微細な切粉が沈殿することで生産効率を下げ、また腐敗による悪臭で作業環境も悪くなるのだとか。
コニテクさんは、そんな切削液を「ろ過」することで「切削液の廃棄ゼロ」を目指す会社です。
とても盛り上がったゼミKYOTO会社見学会の一部をお届けします!
【会社概要】
会社名:コニテク株式会社
会社設立:2006年3月
役員:代表取締役 松田 裕/取締役 中町 尚美
従業員:9名
事業内容:「切削液の廃棄ゼロを目指す!」をスローガンとし、マイナス圧力を利用し精密なフィルタリングを可能にした、マイクロキャッチろ過装置を開発、産業廃棄物(廃油)の削減を行うことで、脱炭素社会への貢献を目指しています。
マイクロキャッチろ過装置以外には、自動機の設計製造メーカーとして、高圧洗浄機・フィルムラップ超仕上げ加工機・ワークストッカー等を商品化しております。
営業品目:
真空ろ過装置
フィルムラップ超仕上げ装置
洗浄装置
ワークストッカー
自動機の設計・製作 ※部品加工
オフィシャルサイト:https://www.konitech.kyoto.jp/
YouTubeチャンネル:https://www.youtube.com/@CatchCleanFuture
スラッジを除去し切削液をロングライフ化!
〜加工精度の安定・刃具寿命の延長・腐敗を防いで悪臭を撃退〜
松田:当社の切削液ろ過装置『マイクロキャッチ』を説明する前に、まずこちらの動画をご覧ください。これは切削加工中の動画で、刃具に吹きかけられている液体が切削液です。切削箇所の潤滑、冷却、防護などが主な目的で、工作機械のタンクに入れられて繰り返し使用され、大体夏と冬の年2回くらい廃棄して新しい切削液に入れ替えるところが多いです。
恵里:使い捨てではないんですね。
松田:そこで問題になるのが、切削液の性能の低下です。大きな切粉なんかはコンベアで排出されますが、細かいものは除去しきれずに戻って来るので、タンクの底にスラッジ(微細な切粉)が沈殿していく状態になっています。そうすると、ポンプで切削液と共にスラッジも吸い上げられますので、刃具にかかる抵抗が大きくなり加工精度が低下します。ミクロン大の加工精度を求められるのに、吹きかけられる液の中にミクロン大のごみがあったら当然精度が出ませんよね。また、抵抗が大きいということは刃具寿命も短くなります。そして、スラッジが浮いた切削液は微生物(バクテリア)が発生し腐敗します。これからの時期は特にですが、切削液が腐敗すると悪臭が強く出ますので、作業環境が非常に悪くなるんです。
当社の『マイクロキャッチ』は、そうした問題の原因になるスラッジを取り除いて、切削液を綺麗な状態で維持し「切削液のロングライフ化」をすることのできる切削液ろ過装置です。
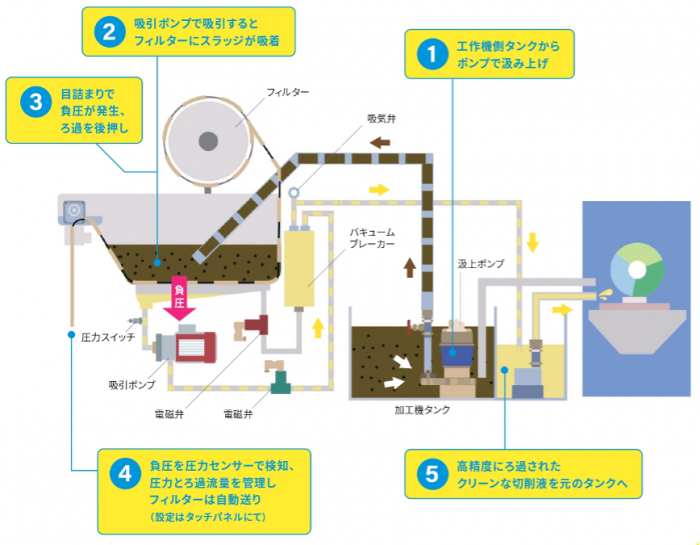
松田:工作機に取り付け、工作機側のタンクから切削液を汲み上げてフィルターでスラッジを除去、浄化された切削液を再び工作機側のタンクに戻す循環式のろ過装置です。高度な技術でろ過する事で新液に近い清浄度を保つので、加工精度を安定させ、機械の刃具寿命を伸ばし、微生物(バクテリア)も発生しないので切削液の腐敗も防ぐ事ができます。
切削液の交換自体が不要に!
〜廃棄コスト、CO2排出量を大幅削減〜
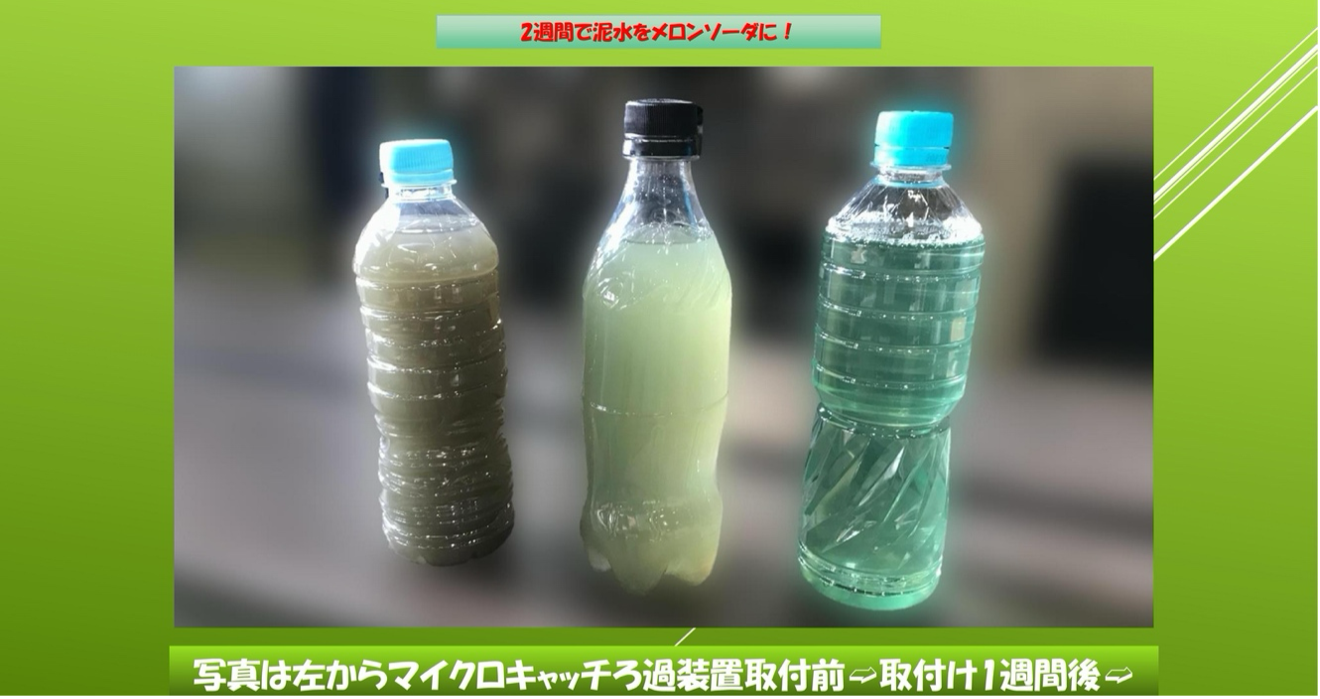
松田:こちらは実際の切削液の画像で、一番左のボトルがろ過前の切削液、真ん中がマイクロキャッチ取付後一週間、一番右が二週間経過したものです。この状態を維持するので、年2回の切削液の交換も不要になります。
恵里:交換自体をしなくて良くなるんですか?
松田:はい。通常、使用した切削液は産業廃棄物になりますので、お金を払って引き取ってもらうことになります。例えばタンク容量が2,400Lのものを処理する場合、切削液2,400Lの他に、汚れたタンクの中を清掃するために水を1,000L使用して、合計3,400Lが産業廃棄物になります。仮に処理費用がリッター70円とすると約24万円、プラス作業人数分の人件費が掛かりますね。また、作業の間工作機器は止まりますし、その後工場の保全にも日数が取られます。勿論廃棄したら新しい切削液を入れないといけませんから、仮にリッター750円で240L入れたとすると18万円。諸々を合わせると、1回で大体54万円、年2回で大体108万円ほど掛かるかなと思います。これはだいぶ前のデータなので、今はもっと値段が上がっているかもしれません。
恵里:結構かかるんですね。
松田:ある程度で掃除をしないとポンプが壊れるなどのトラブルも出てきますので、この辺で捨てようというのが大体年2回という会社が多いと思います。ただ、中には全然捨てていないというところもあって、沈殿物をスコップで掬って使っているようなケースもあります。でも、そうなると沈澱物の影響で加工精度が落ちていますので、例えばロットで加工していたりすると、不良品が取引先まで流れてしまってロット見直しになったりという可能性があります。そのためある程度の量で出しているところは、やはり神経質に交換をされていますね。
恵里:切削液自体をろ過することで、その費用自体をかからなくできるわけですね。
松田:また、切削液の消費量は年間13万トン、使用後の廃油にいたっては年間42万トンと言われています。それらは産業廃棄物として焼却処理されるため、その時に大量のエネルギーが消費され、大量のCO2を排出することになります。捨てるのにもコストがかかり、捨てたら捨てたで環境にも良くない。『マイクロキャッチ』で切削液をロングライフ化することで、両方の問題を解消することができます。
あえて目詰まりさせることでフィルターの精度を上げる
松田:どうやってここまで切削液をろ過しているかというと、タンクの底の部分から沈殿物を全てろ過装置側に供給し、フィルターを「目詰まりさせながら」ろ過しているというのが特徴です。敢えて粗めのフィルターを使用し、大きいゴミから先にろ過していくことで、目詰まりして徐々にフィルターの穴が小さくなっていく。そこに何回も切削液を通すことでフィルターの精度を上げていき、より細かいゴミまでろ過できるようになっていく。最終的に全部目詰まりして埋まったらフィルターを交換するというろ過方法なんです。先ほどの画像で、綺麗になるまで一週間から二週間かかっていたのはそのためです。
恵里:フィルター自体は、一般的なろ過フィルターなんですか?
松田:はい。ごく一般的なフィルターで、お客様の用途に合わせて5μ・2μ・1μ・0.7μ・0.5μの5種類から合うものを選んでいます。というのも、細かいフィルターを使用すれば一気にろ過することはできるんです。開発時に色々なフィルターを試したんですが、当初は私たちもろ過精度を上げるために、とにかく細かくしようという方へ頭がいっていました。そして確かにろ過できるんですが、一回切削液を通すとフィルターが使えなくなってしまうんです。そんなにフィルターにコストを掛けていてはとても成り立たない。そこで発想を転換して、今度は粗くしていったんです。
先ほどの図解を見ていただくとわかりやすいと思いますが、装置の上部に巻物状のフィルターがセットしてあり、そこから装置の内部を通って切削液をろ過します。徐々に目詰まりしていくと吸引ポンプとフィルターの間で負圧が強くなっていきますので、圧が設定値まで強まると完全に目詰まりしたということで、自動でフィルターが装置の外へ送られるという仕組みです。この時、装置内の全部のフィルターが排出されるのではなく、端の負圧が設定値を超えた部分のみなので、フィルター全体を効率的に使用することができます。
切削液腐敗の二大要因、スラッジと浮上油
〜『リキッド・クリーニングボール』で浮上油も残さず吸引〜
松田:先ほど切削液が腐敗して悪臭を放ち作業環境が悪化するという話をしましたが、腐敗の原因にはスラッジともう一つ浮上油というものがあります。工作機械を作動させるためには工業用の潤滑油が必要で、装置をすべらせながら動かす摺動面に自動で吹きかけながら動いています。その摺動油(しゅうどうあぶら)が切削液に混ざってしまうんです。それが切削液の上に浮いているのが浮上油で、これは水中のポンプではなかなか吸引できないので、タンクを上から見ると真っ黒になっていることがあります。スラッジとこの浮上油が、切削液腐敗の二大要因になっています。そこで、この浮上油を吸引するために『リキッド・クリーニングボール』というオプションもつけることができるようになっています。
松田:吸い口にボールのような浮き輪を3つ取り付けることで、水面に浮く油をポンプで吸い込むことができる装置です。これとマイクロキャッチのポンプで上下から切削液を吸引することで、タンクの中を効率的に浄化することができます。
恵里:この取り除いた浮上油は、切削液とは別に捨てなければいけないんですか?
松田:浮上油は切削液と混ざった状態でマイクロキャッチの中に吸引されますので、フィルターがスラッジと一緒に油も吸着して排出してくれます。切削液は浄化された状態を維持できます。
「切削加工や機械加工のベースは『ろ過』や!」
〜目指すは切削液廃棄ゼロ!〜
松田:私はずっとサラリーマンをやっていまして、今のコニテク株式会社を起こしたのは50歳の時です。サラリーマン時代は、自動機メーカーや部品加工メーカーで装置の営業と設計、それから製造・購買・アフターサービスなどをやっていました。起業当初は、大体大手の会社さんから「こういう自動機をつくってほしい」という仕様書をいただいて、それを設計して開発するというような形で進めていたんですが、リーマンショックのときに大手さんが全部、設備投資をストップされたので、我々もやることがないというようなことで落ち込みまして。
恵里:ろ過装置はやっていなかったんですか?
松田:ろ過装置もやってはいました。ただ、ろ過装置というのは小ぶりで売上金額も100〜200万円ほど、一方自動機の場合は1,000万円とか 1,500万円とか。設計的にも動くような機械のほうが面白くて、そちらの方を中心にやっていました。しかしリーマンショックになって、日本中で営業をしたのですがなかなか自動機の仕事が取れなくなってしまい、それで中国にも行ったりしたのですが自分たちの会社には合いそうもない。ただ、中国にしろ日本にしろ、「仕様を受けて機械を作りますよ」というより、自分たちの製品を持って「こういう機械ですよ」という方が有利なんじゃないかなと感じました。
それで目をつけたのが、切削液のろ過装置でした。これは元々大手さんのプロジェクトに私たちも参画してやっていたものなのですが、切削液をろ過することで製品の不良率を低減できることであったり、加工スピードを高速化、併せて刃物の寿命が延びるということ、液の異臭を防いだり、生産効率がぐんと上がるということが分かってきまして、「切削加工や機械加工のベースは『ろ過』や」と。
恵里: それが現在のマイクロキャッチへの転換になったんですね。
松田:大手さんからも「これは、あんたのところの商品や」「だから、これで売り出したらええ」と背中を押してもらい、現在の流れになりました。とはいえ、その当時はかなり大型の装置でしたので、そこからはかなりの試行錯誤を繰り返しました。小型化するとどうしても処理能力も低下してしまうので、フィルターの使い方にも工夫が必要になります。先ほども言ったように敢えてフィルターを目詰まりさせる仕組みなので、マイナスの圧力がタンクの中をグッと圧縮します。その圧縮したものを上手く解放できないとタンクが割れてしまったりもします。しかしタンクの鉄板を厚くすれば、それだけ値段もぐんと上がってしまう。何回も失敗しながらやっと今の形になり、特許も取りましたので、晴れて「これを自分たちの製品としてやっていこう」というものができました。
その後、SDGsやカーボンニュートラルといった地球環境の課題が注目されるようになり、切削液のろ過はその問題にも貢献できるなと。産業廃棄物として焼却処理されていた切削液をロングライフ化することでそれだけに二酸化炭素排出量の削減になります。そこで2、3年前からは、「切削液廃棄ゼロを目指そう」というのを会社の 1つのポリシーにしています。経営理念には、「『もっとこうなったらいいのに』というのを追求し、具体化しサービスや商品を提供する」という言葉を入れました。「もっとこうなったらいいのに」という発想は、仕様書を頂いてつくる自動機ではなかなか入れられませんでした。自分たちの製品であるろ過装置は、「もう少しこうなったら、もっとお客さんが喜ぶ」とか「もっとここが改善できたら、お客さんに提供できる」と考えながら、一つの技術を深く追求していくことができるので、会社のメンバーの面白いと感じていると思います。
今後の課題は営業
〜ゼミKYOTOメンバーとの意見交換〜
松田:今、このろ過装置『マイクロキャッチ』を主軸に据えて、少しずつ伸びてきています。ただ、私たちはもともと設計を中心とした会社なので、営業が下手なんです。今後の課題がそこで、今スモールサン・ゼミKYOTOで色々と話を聞いて勉強させてもらっています。
ここで見学に参加したゼミKYOTOメンバーとの意見交換が行われ、かなりの盛り上がりに!
「『ろ過』を切り口にするなら、切削液以外でもニーズがあるのでは?」
「建設現場では汚れた廃液の処理で近所とトラブルになる場合があるので、結構ニーズがありそう」
「印刷業界でも水の処理は課題になっている」
などなど具体的な意見に始まり、
「ChatGPTを使えば、『ろ過』が必要な業種や売り込み方を提案してもらえるから、それも活用した方がいい」
といった提案も。
その後、工場で『マイクロキャッチ』の実物や製造工程を見学。
ゼミKYOTOの会社見学企画第1回はとても盛り上がり、第2回以降も企画中とのこと。引き続き、そちらもご期待くださいませ!
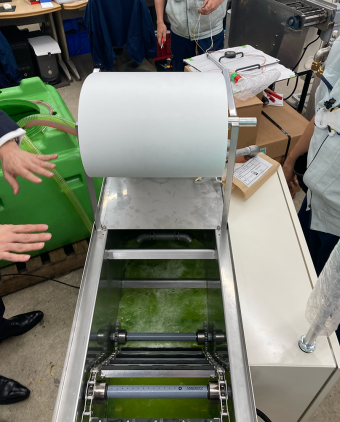
